Our Services
LYNwave has been developing optimized solutions of customized antenna, thermal, mechanical and outdoor enclosure designs based on reliable simulation technologies, providing comprehensive high-performance antennas and services such as 3D printing, throughput testing and Wi-Fi test house testing to realize your IoT programs.
Home » Service » System Integration Service » 3D Printing Service
3D Printing Service
LYNwave’s 3D printing service can help your project with…
Comparing to traditional manufacturing processes, the 3D printing technology allows us to produce complex geometries with fast speed, low fixed setup costs and less material wastage. Before receiving the markdown samples, which our customers will send us after they design IP mechanical, we can 3D print the antennas first. It helps us to save time at an early stage, so that we can do a few more sample runs to test and fine-tune the antennas.
It has the significant benefits of speeding time-to-market, offering better opportunity to test and improve each iteration. Several cycles of the prototyping process can be accomplished within a week or even in the same day, as it can improve the effectiveness of communication throughout the design cycle. With our 3D printing service, we can make the antennas more accurate and speed up the entire engineering process.
Reduce Time-to-Market with a Cost-Efficient Product
Since competitive positioning requires that development and introduction be quick especially in the consumer market, we can use 3D printing to achieve that. A 3D printer can create new versions of antennas from slightly adjusted digital files much faster than could any traditional tooling-based prototyping process. Speeding up the design cycle can cut lead times and costs, make products turn out better, and get to market faster, saving costs from longer and more tooling-intensive traditional workflows.
Test and Fine-Tune the Antennas While Improve Effective Communication
Creating a functional prototype with actual size can allows us to have better understanding of the design. We can evaluate and improve any manufacturing issues or usability risks while still in the pre-production stages. As each prototype built up, any small tweaks or large adjustments become easier to understand for both sides of our customers and LYNwave. This process can close communication gaps with more efficient conversation.
The 3D printing methods LYNwave uses
- FDM (fused deposition modeling)
FDM, also known as FFF (fused filament fabrication), is a 3D printing method where materials (thermoplastic filaments) are extruded through a nozzle onto a tray to build a part layer by layer from a bottom up. With FDM printing, a wide variety of materials can be printed with relatively few modifications, meaning that a single FDM 3D printer can produce parts with different properties and appearances just by changing the type of filament.| Raise3D Pro2 3D Printer |
- Electronic Driven Dual Extrusion with 4× Increased Torque Performance for Larger Spool Sizes
- Massive Build Volume (12 × 12 × 11.8 inch)
- Diverse Filament Compatibility (Temp.: Up To 300°C)
- Filament Run Out / Power Loss with Resume
- Camera Monitor System
- HEPA Air Filtration System
- Wireless Compatibility
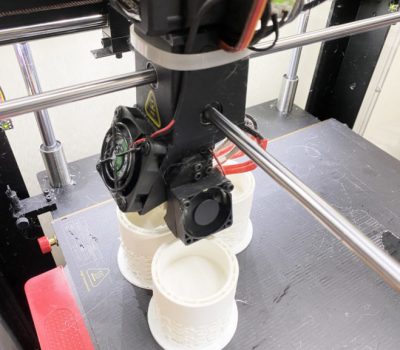
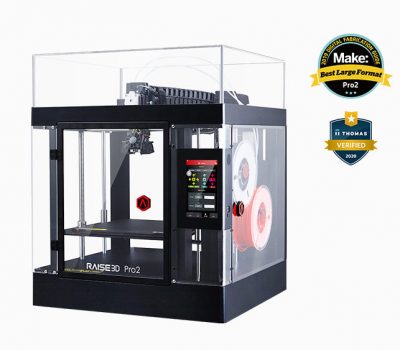
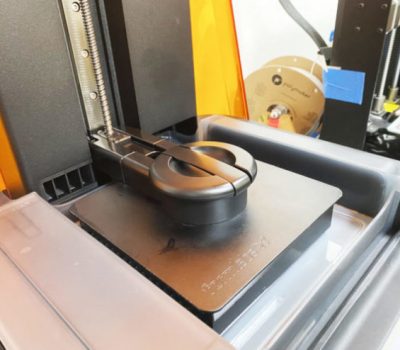
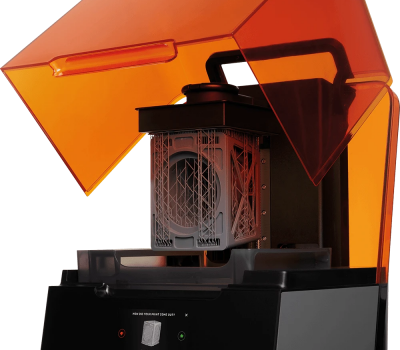
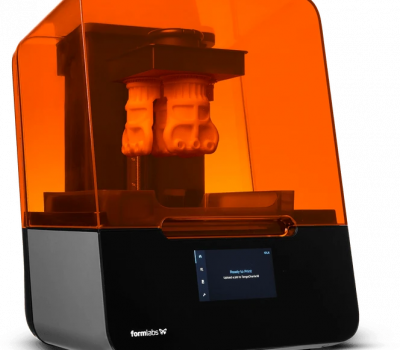
- SLA (stereolithography)
→LFS (low force stereolithography)
SLA, also known as vat photopolymerization or resin 3D printing, is a 3D printing process that converts photosensitive liquid into 3D objects in a layer-by-layer fashion using a low-power laser and photopolymerization. Prototypes can be created with extremely high quality, such as finely detailed features, complex geometrical shapes, and smooth print surfaces.Based on Inverted SLA, which means the process is turned upside down, Formlabs developed a new technology called LFS, an upgraded form of Inverted SLA. The 3D printer combines a flexible tank (while SLA has a rigid tank) with a scalable LPU (light processing unit) which provides linear illumination to brings out better part detail and surface finish. While SLA has a problem with peel forces, which the forces exerted on parts during the printing process makes supports difficult to remove, LFS allows for light-touch supports that can be easily peeled away and aide clean part removal. Comparing to SLA 3D printing, LFS is more accurate, reliable, faster, and easier to maintain.
| Formlabs Form 3+ 3D Printer |
- Increased Laser Power (250 mW)
- Rapid Print Speeds with Up To 40% Faster Printing
- Easy Support Removal
- Simplified Automated Seamless Post-Processing Solutions
- Improved LPU Stabilization with LFS technology (An Upgraded Form of Inverted SLA)
- Flexible Tank with Linear Illumination
- Massive Build Volume (5.7 x 5.7 x 7.3 inch)
One of the most valuable advantages of our 3D printing service is the ability to test and compare different design ideas. Using 3D printing for rapid prototyping can revolutionize the workflows on both customers’ and LYNwave’s side, which also saves cost and time combined with a simpler design testing process. Both FDM and SLA printing can help you with your project. We will make sure to satisfy your requirements by providing our 3D printing service to you.
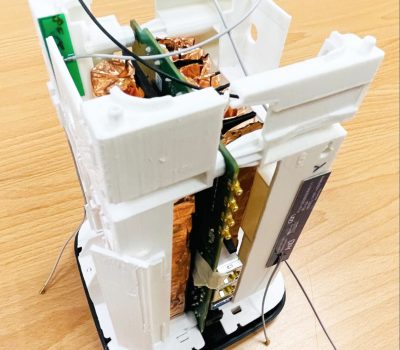
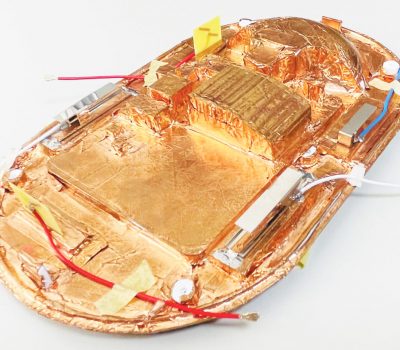
If you’d like to learn more about our 3D printing service, feel free to contact us to have discussion with us on your needs. LYNwave is looking forward to supporting you throughout the process.